

To speed up the process of EMI filter design to meet EMI specifications, this article shows how conducted EMI noise analysis and filter design can be easily estimated and prebuilt using ADI’s LTpowerCAD ® program. Unfortunately, EMI analysis and filter design can be a difficult task, typically requiring a time-consuming iterative process of design, build, testing, and redesign-that is, assuming one has proper test equipment. To meet these limits for a switch-mode supply, one must first quantify its EMI performance and, if necessary, add proper input EMI filtering to attenuate the EMI. Because of this, many standards have arisen to set acceptable limits on EMI. The problem is that high frequency noise can couple to other devices in the system, degrading the performance of sensitive analog or digital signal circuits. Fast turn-on and turn-off of power transistors create sudden interruptions of current flow, resulting in high frequency voltage ringing and spikes. For example, the input side switch current of a typical buck converter is a pulsating current rich in harmonic content. This is commonly referred to as electromagnetic interference (EMI), EMI noise, or just noise. One side effect of the proliferation of switch-mode supplies is the noise they produce. Switch-mode power supplies are used throughout modern electronics systems mainly because of their high efficiency power conversion. However, not simulating isn't really a viable option these days because you will definitely significantly improve your chances of getting close to a pass by doing so and, pretty much, all from the comfort of your desk.Speed Up the Design of EMI Filters for Switch-Mode Power Supplies $$\boxed$$īut, there's no guarantees you will pass your conducted emission test because reality is never the same as a simulation. The very first thing I would do is simulate the circuit in order to understand the current consumption and harmonics in the worst case loading scenario. The specific application I am designing a filter for is a 24V, 120Wįlyback converter in the consumer electronics market.
Ti filter designer how to#
My design (and the reference designs I am using) does not feature any Y-Caps because the line cord does not have an earth-ground connection prong.īasically, I just need some help on how to initially determine the values for these components. TI's application notes on the filter inductor put it in the context of a CLC filter, which is confusing because I thought we chose the input/smoothing capacitor value based on the input power and not the required attenuation. I will admit that I am not sure how to calculate the power consumption of a capacitor in this context.

X capacitor selection for SMPS power supply I believe the X-Cap choice is based on power consumption and power factor (according to post linked below)? You then verify this choice experimentally.
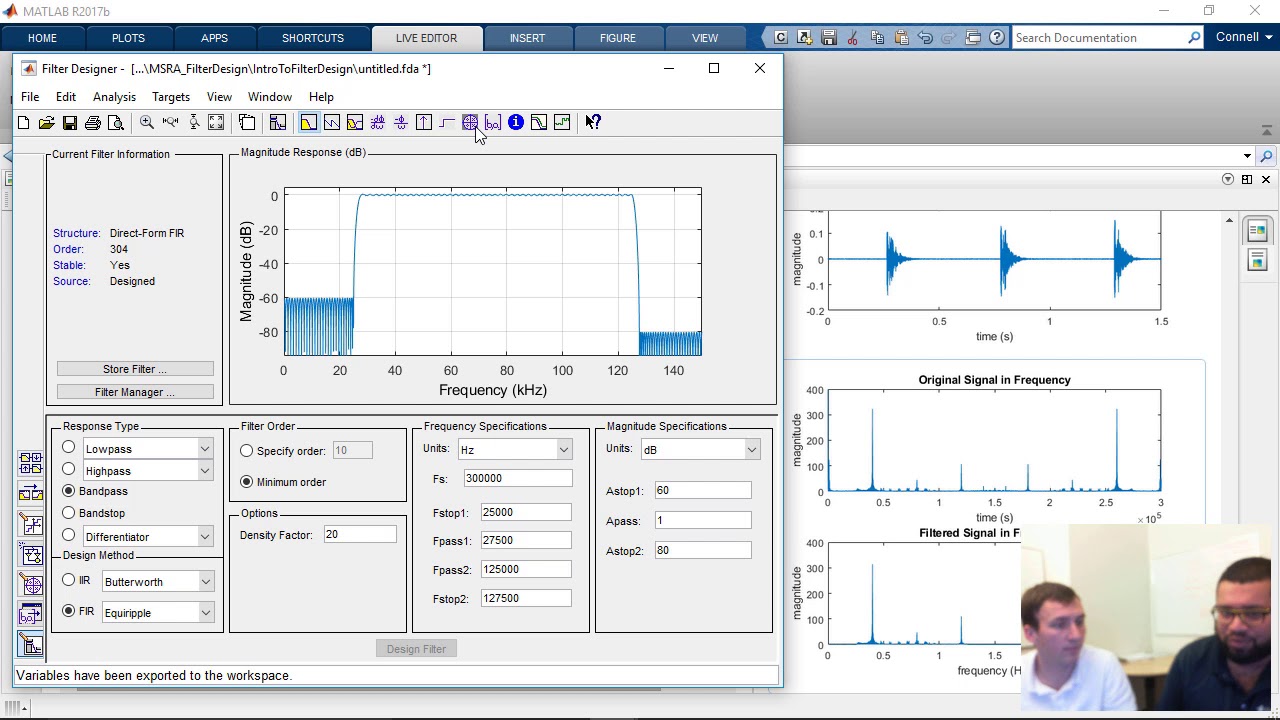
I believe that the common-mode choke is first selected based on its attenuation curve and what you think the the trouble frequencies will be. The CM Choke and Y-Caps are in charge of attenuating the common-mode noise, while the Y-cap and Filter inductor are in charge of attenuating the differential-mode noise. The input EMI filter has 4 main components: Common-Mode choke, X-Cap, Y-Cap, and Filter Inductor. My basic question is "How do you select the component values for your EMI input filter?" The specific application I am designing a filter for is a 24V, 120W flyback converter in the consumer electronics market.

I have been reading and watching TI's material on EMI input filter design, and I have a few questions.
